The history of the mining conveyor belt is a testament to the evolution of industrial technology and materials science. Initially crafted from basic natural materials like leather and canvas, these belts served as rudimentary tools for transporting mined materials from deep underground to the surface. As the demands of the mining industry grew, so did the need for more durable and efficient conveyor systems. The introduction of rubber and metal belts marked significant advancements, offering increased durability and capacity to handle heavier loads. Over the years, developments have included belts made from synthetic materials like polyester and nylon, which provide enhanced strength, flexibility, and resistance to environmental factors. Today, mining conveyor belts vary in design and material to suit different mining environments and operational needs.
Contents
Development of Materials
The evolution of materials used in conveyor belts has been marked by significant technological advancements and innovations, particularly in the transition from traditional materials to modern composites. This transition has not only enhanced the performance of these belts but also broadened their applications in mining and other heavy industries.
Transition from Traditional Materials to Modern Composites
1. Early Materials:
Initially, conveyor belts were made from natural materials such as leather, canvas, and rubber. These materials, while effective for light to medium loads, lacked the durability and strength needed for the heavy-duty requirements of modern mining operations.
2. Introduction of Synthetic Materials:
The introduction of synthetic materials such as polyester, polyamide (nylon), and polyvinyl chloride (PVC) marked a significant advancement. These materials brought improvements in terms of strength, flexibility, and resistance to abrasion, oils, and various chemicals.
3. Development of Composites:
The real breakthrough came with the development of composite materials, which combine different synthetic fibers or combine synthetic materials with natural fibers to achieve superior properties. Composites in conveyor belts often involve layers of different materials that provide high tensile strength, excellent troughability, and low stretch, all critical for high-capacity and long-distance conveying.
Adoption and Evolution of Steel Cord and Nylon in Mining Belts
1. Steel Cord Conveyor Belts:
Steel cord conveyor belts represent a pivotal development in mining operations. Introduced as a solution for long-distance, high-load applications, steel cords offer unmatched tensile strength and durability. The steel cords, made from strands of high-carbon steel, are laid longitudinally and are embedded in a rubber matrix. This design minimizes elongation under load, making these belts ideal for the primary conveyance lines in mines.
Over the years, the technology behind steel cord belts has evolved to improve splice strength, corrosion resistance, and flexibility, enhancing their lifespan and reliability in harsh mining conditions.
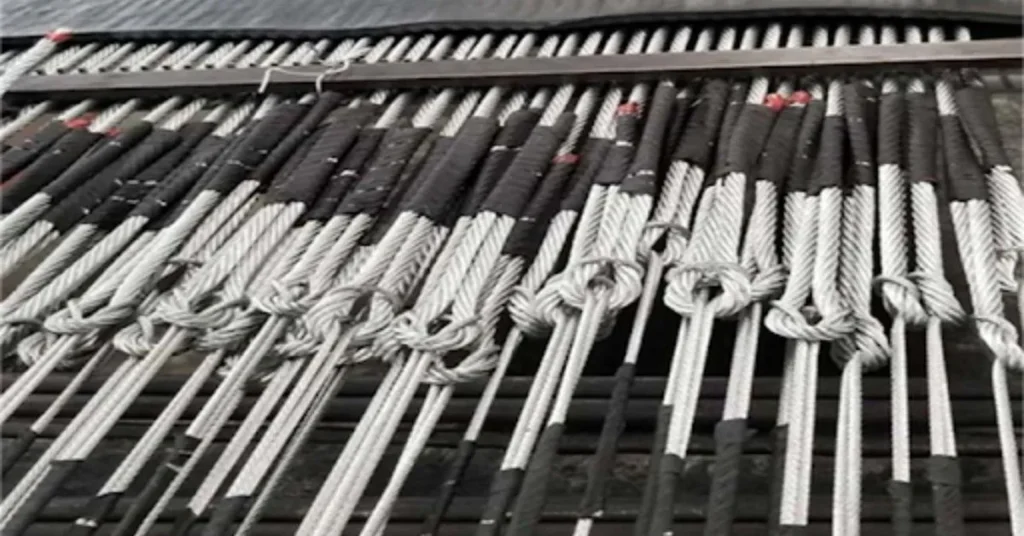
2. Nylon Conveyor Belts:
Nylon, known for its excellent impact and abrasion resistance, was adopted for conveyor belts to handle medium-duty tasks. Its high tensile strength and elasticity make it suitable for mining operations that involve changes in elevation and require belt flexibility.
Innovations in nylon belt technology have focused on improving the weave design and coating techniques. Modern nylon belts feature advanced fabric weaves that provide better load distribution and enhanced resistance to ripping and tearing. Additional treatments have also been developed to increase resistance to oils, chemicals, and extreme temperatures.
The development of conveyor belt materials from traditional options to advanced composites like steel cord and nylon has significantly impacted the efficiency and safety of mining operations. These materials have evolved to meet the increasing demands of the mining industry, ensuring that conveyor belts not only handle the heavy load but also withstand the tough environmental challenges of modern mining environments.
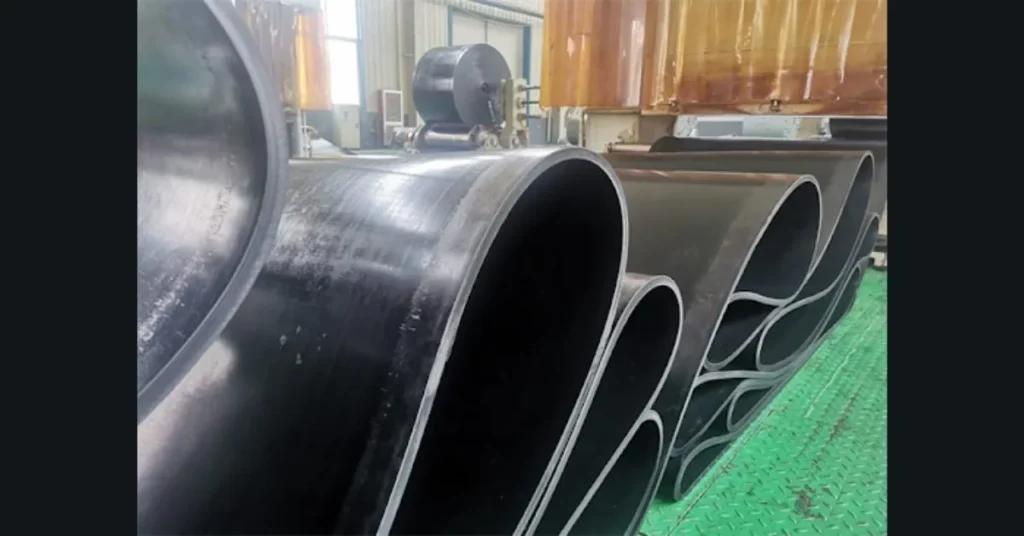
Technological Advancements
The field of mining conveyor belts has witnessed substantial technological advancements, particularly in the development of steel cord and nylon technologies. These innovations have been pivotal in optimizing the performance, durability, and overall efficiency of conveyor systems in harsh mining environments.
Innovations in Steel Cord and Nylon Technologies
1. Steel Cord Conveyor Belts:
Advanced Cord Composition: Recent advancements in steel cord technology include the use of higher-grade steel and improved cord structures. These modifications have resulted in cords that are not only stronger but also more flexible, allowing the belts to handle greater loads and operate over longer distances without significant wear.
Enhanced Rubber Matrix: The rubber compounds used in steel cord belts have also evolved. Modern formulations are designed to provide better adhesion between the cords and the rubber, increased resistance to heat, and reduced susceptibility to tearing. This has notably extended the lifespan and reliability of these belts under extreme mining conditions.
Corrosion-Resistant Coatings: To combat the issue of corrosion, which can weaken steel cords, new belts are treated with specialized coatings. These coatings protect the steel cords from harsh elements, including moisture and corrosive chemicals prevalent in mining environments.
2. Nylon Conveyor Belts:
Improved Fiber Technology: Nylon belts have seen innovations in fiber technology that enhance tensile strength and abrasion resistance. The introduction of composite fibers, where nylon is blended with other synthetic materials, has led to belts that maintain flexibility while significantly increasing durability.
Thermal and Chemical Treatments: Advances in thermal and chemical treatments have improved the environmental resistance of nylon belts. These treatments make the belts more suitable for a range of temperatures and reduce degradation from chemical exposure, which is common in mining processes.
Eco-friendly Manufacturing: There is a growing emphasis on reducing the environmental impact of nylon belt production. This includes processes that consume less energy and produce fewer emissions, aligning with the global push towards sustainability in industrial materials.
Impact on Performance and Durability
1. Optimized Load Handling: Both steel cord and nylon conveyor belts have been engineered to handle higher loads with minimal maintenance. The structural improvements in these belts allow them to support heavier weights, distribute loads more evenly, and reduce the strain on conveyor components.
2. Enhanced Lifespan: The technological enhancements in material composition and manufacturing processes have significantly increased the lifespan of these belts. This durability is crucial in mining operations, where replacing conveyor belts frequently can be costly and disruptive.
3. Improved Safety and Reliability: With stronger materials and better resistance to environmental hazards, the risk of belt failure has decreased. This reliability is essential for maintaining continuous operations in mining, minimizing downtime, and ensuring worker safety.
4. Energy Efficiency: Innovations in belt design, particularly in terms of reducing weight and minimizing friction, have led to more energy-efficient conveyor systems. These systems require less power to operate, which not only reduces energy costs but also lessens the environmental impact of mining operations.
These technological advancements in mining conveyor belts, specifically in steel cord and nylon technologies, demonstrate a clear trajectory towards more efficient, durable, and sustainable mining operations. As these innovations continue to evolve, they promise to further enhance the capabilities and benefits of conveyor systems in the mining industry.
Future Trends
As we look ahead, the future of conveyor belt technology in mining appears poised for even more groundbreaking developments. Advancements are expected to center around the integration of new materials and the application of smart, Internet of Things (IoT) enabled systems that further enhance efficiency and sustainability. Here’s a detailed look at the upcoming trends that are likely to shape the next generation of conveyor belts in the mining industry.
Predictions on Future Materials and Technologies
1. Advanced Composite Materials:
The ongoing development of composite materials promises conveyor belts that are even lighter, stronger, and more durable. These composites will likely include nano-materials that offer exceptional strength-to-weight ratios and enhanced properties such as heat resistance and self-healing capabilities after minor damages.
2. Environmentally Friendly Materials:
As sustainability becomes increasingly important, the demand for eco-friendly materials in conveyor belts is expected to rise. Future materials may be fully recyclable or biodegradable, reducing the environmental footprint from production, usage, and disposal stages. Moreover, there’s potential for materials designed to reduce energy consumption by minimizing friction and resistance during operation.
3. Temperature and Chemical-Resistant Technologies:
Enhanced resistance to extreme temperatures and corrosive chemicals will be crucial, especially for operations in harsh environments. Innovations may include the development of belts that can withstand extreme cold and heat without losing performance, as well as coatings that protect against chemical degradation.
Potential for New Materials and Smarter, IoT-Enabled Belts
1. Integration of IoT and Sensor Technology:
The future of mining conveyor belts is strongly tied to the integration of IoT technologies. Belts equipped with sensors can continuously collect data on performance metrics such as speed, temperature, load, and belt wear. This data can be used not only for real-time monitoring and adjustments but also for predictive maintenance, significantly reducing downtime and extending the belt’s life.
2. Real-Time Communication and Control:
IoT-enabled belts will likely be part of a larger automated system where real-time communication between the belt and control systems enables automatic adjustments based on changing conditions. For example, a belt could automatically adjust its speed based on load weight or weather conditions to optimize energy use and prevent wear and tear.
3. Advanced Monitoring Systems:
Future conveyor systems could incorporate more advanced monitoring technologies, including visual recognition systems that use AI to detect anomalies along the belt line that human inspectors might miss. This could lead to immediate corrective actions, enhancing both efficiency and safety.
4. Sustainability and Life Cycle Management:
Innovations are expected to focus not just on operational efficiency but also on the full lifecycle management of conveyor belts. This includes the use of materials that are easier to manufacture and recycle, and systems designed to reduce overall energy consumption throughout their operational life.
The convergence of advanced materials science, IoT technologies, and increased environmental awareness is set to revolutionize the way conveyor belts are used in the mining industry. These future trends highlight a shift towards more sustainable, efficient, and highly intelligent conveyor systems that promise to transform the operational dynamics of mining.
Impact on Mining Operations
Advancements in conveyor belt technology have significantly transformed operational efficiencies in the mining industry. These improvements not only facilitate the effective and swift transport of materials but also enhance overall production timelines, safety, and environmental sustainability. Let’s explore how these technological improvements have been applied and their impact through specific case studies in various mining environments.
Transforming Operational Efficiencies
1. Increased Production Speeds:
Modern conveyor belts, equipped with advanced materials and technologies, handle higher volumes of material more quickly than older versions. This capability allows mines to increase their output without compromising the integrity of the transported materials.
2. Reduced Downtime:
With the integration of smart sensors and durable materials, modern conveyor systems can predict and prevent failures before they occur, significantly reducing downtime. The ability to perform preventive maintenance based on real-time data ensures that operations continue smoothly with minimal interruptions.
3. Lower Maintenance Costs:
The durability and enhanced design of contemporary mining conveyor belts mean that they need less frequent repairs and replacements. This reduces the long-term maintenance costs associated with mining operations and allows for better allocation of resources.
4. Improved Worker Safety:
Enhanced safety features, such as automatic shut-offs and emergency stop mechanisms, integrated into modern conveyor systems help protect workers from common hazards associated with belt malfunctions.
Case Studies on Significant Improvements
1. Case Study in an Australian Iron Ore Mine:
In this large-scale operation, the introduction of high-strength steel cord conveyor belts allowed the mine to double its output. The belts’ superior tensile strength and low elongation under load reduced belt slippage and splice failures, which had frequently halted production on older belts. As a result, the mine saw a 15% reduction in downtime.
2. Case Study in a Canadian Gold Mine:
A Canadian gold mine implemented a conveyor belt with advanced nylon composites and real-time monitoring sensors. This upgrade led to a 20% increase in material handling efficiency and a 30% decrease in maintenance costs. The sensors helped the mining company predict belt wear and tear, optimizing maintenance schedules and reducing unexpected breakdowns.
3. Case Study in a South African Coal Mine:
This mine switched to a conveyor belt system that used a specially designed rubber compound to withstand the abrasive nature of coal. The new system reduced conveyor-related incidents by 40% and increased coal handling efficiency by 25%. The belt’s enhanced durability and abrasion resistance ensured consistent operation in the harsh mining environment.
These case studies exemplify how significant advancements in conveyor belt technology can result in tangible improvements in mining operations. The adoption of stronger, smarter, and more efficient conveyor systems not only boosts productivity but also enhances safety and reduces the environmental impact of mining activities. As technology continues to advance, the mining industry stands to gain even more, driving further efficiencies and innovations in global operations.